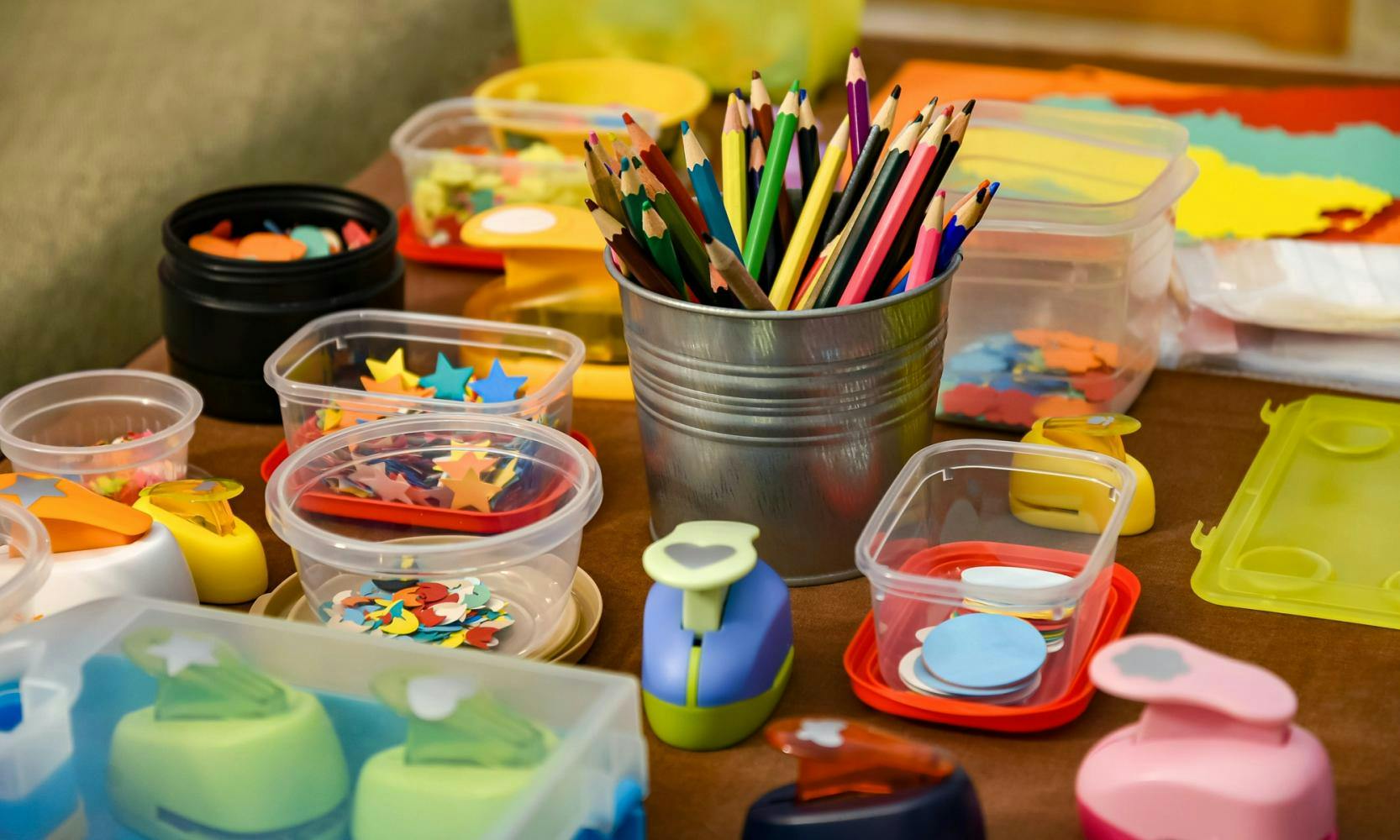
Plastic Boxes: The Benefits You Need to Know (and 10 Reasons to Buy)
- Visibility: Transparent plastic boxes make it easy to see what's inside, giving your products an enhanced appearance and making it easy to find what you're looking for.
- Professional Presentation: Plastic boxes offer great shelf appeal and present your products in a professional manner.
- Strength and Reusability: Plastic is stronger than cardboard, which means your contents won't get squashed, and you can reuse plastic boxes over and over again.
- Waterproof: Unlike cardboard, plastic boxes don't go soggy or fall apart when wet, making them ideal for outdoor use or damp environments.
- Less Prone to Water Damage or Damp: Plastic is less prone to developing mould than cardboard, making it a safer choice for long-term storage.
- Durable and Long-Lasting: Plastic boxes are much more durable and longer-lasting than cardboard, which is really only a temporary solution.
- Oil and Moisture Resistant: Plastic boxes are resistant to oil and moisture, making them ideal for storing items that might leak or spill.
- Popular Choice: Over 53% of all goods are packed using plastic, making it a popular choice for businesses and individuals alike.
- Postage Savings: Plastic boxes are lightweight, which means they can save you money on postage when compared to heavier cardboard boxes.
- Environmentally-Friendly Options: Many plastic boxes are now made from recycled materials and can be recycled again after use, making them an environmentally-friendly choice.
Available in 4 types of plastic, with a range of colour and shape including :
Colours: Transparent, White, Black, Grey, Yellow, Red, Blue, Orange, Green
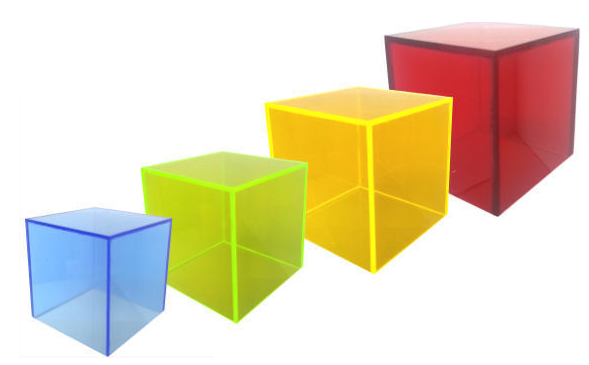
Shapes: Rectangular, Square, Round

Crystal Polystyrene
Plastic Box Guide
What is Crystal Polystyrene Plastic?
Crystal Polystyrene Plastic, commonly known as PS for short, is a versatile polymer utilised in the manufacturing of various products. It is a solid and sturdy plastic with excellent heat resistance, mainly used in products requiring high clarity.
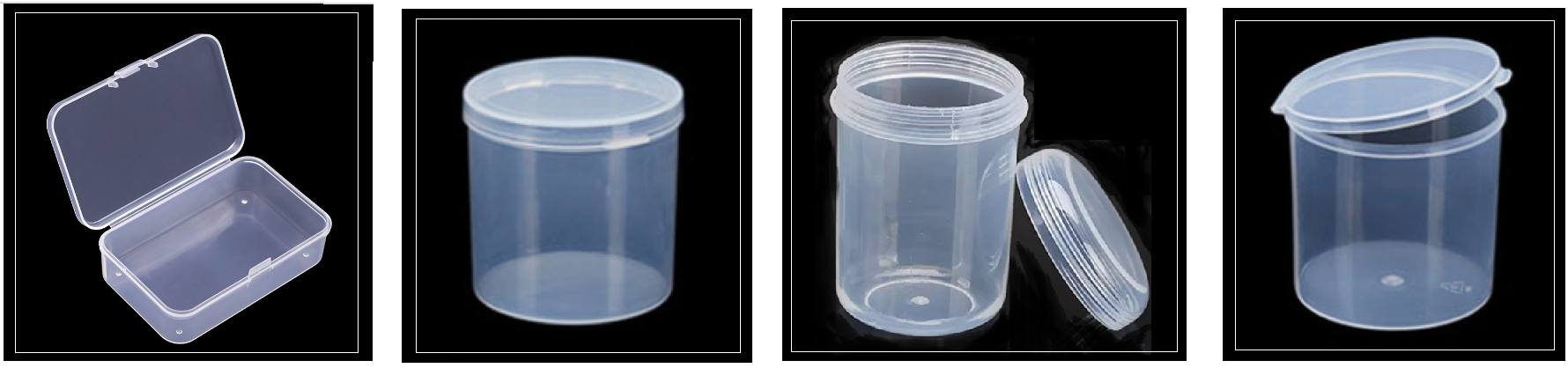
Crystal Polystyrene - What Style of Lid ?
- Regular hinged
- Ball hinged
- List-off/push-fit
- Sliding
Printing Options for Crystal Polystyrene Plastic Boxes
Crystal Polystyrene (PS) is a versatile polymer that offers a clear and hard surface suitable for high-clarity products. When it comes to printing on PS plastic boxes, there are three main options: silkscreen printing, digital printing, and pad printing.
Silkscreen Printing
Silkscreen printing is a stencil-based printing process where ink is forced through a silk or polyester sheet to transfer an image onto the surface of the plastic box. This printing method has been around for centuries, and it is ideal for producing bold and colorful graphics. Each color requires its own silk screen.
Digital Printing
Digital printing is a toner-based inkjet technology that directly prints the image onto the surface of the plastic box without requiring printing plates. Digital printing is known for producing high-quality results, and it allows for easy modification of artwork or messages with minimal additional cost. Short print runs can be cheaper than other printing methods, making it an ideal platform for print-on-demand.
Pad Printing
Pad printing is a process that uses a silicone pad to transfer an image from a laser engraved printing plate onto the surface of a plastic box. This printing method is ideal for printing on difficult shapes that are concave, cylindrical, spherical, or have curved sides.
The pad printing method is popular in the pharmaceutical and medical sectors for printing on products such as coated tablets, gel capsules, syringes, inhalers, insulin pens, catheters, and other medical devices.
How are Crystal Polystyrene boxes made?
Crystal Polystyrene boxes are manufactured by the Injection Moulding method, so each box requires its own dedicated injection moulding tool. Injection moulded boxes can be straight sided or tapered.
The plastic granules are heated and melted, so that they can be injected into a custom-shaped cavity i.e. the mould, where pressure forces the melted resin to form into the required shape of the end product inside the moulding tool, in our case, a plastic box. This method of manufacturing means the plastic boxes are more capable of holding to a tighter dimensional tolerance and with a more uniform wall thickness.
Injection Moulding Explained
Step 1: The mould closes
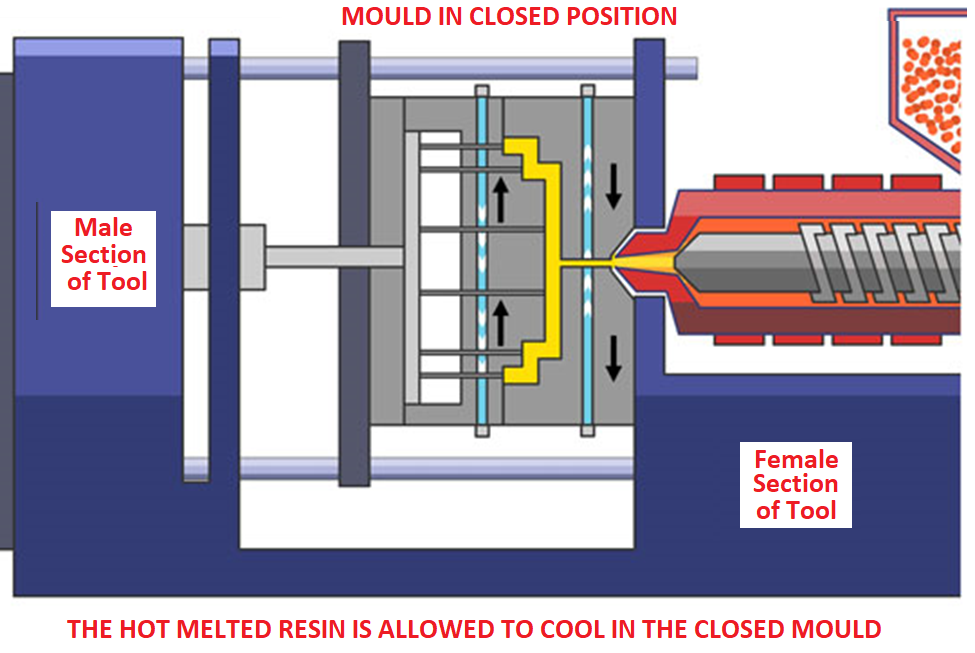
The first step involves closing the mould, which is made up of two halves. The mould is clamped shut and the resin will be injected into it.
Step 2: The injection stage
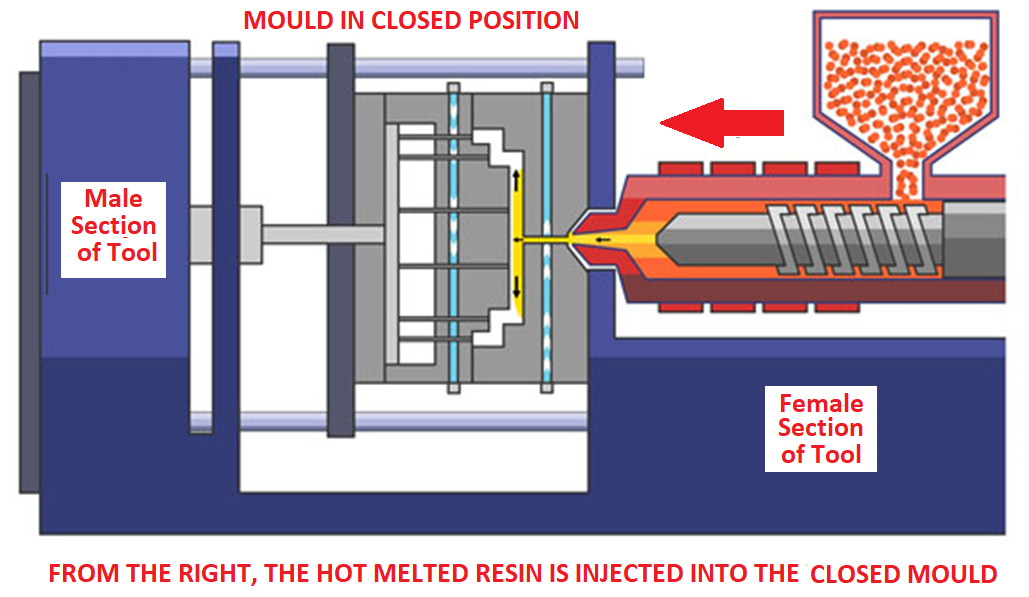
The heated plastic resin is injected into the mould. As the melt enters the mould, the displaced air escapes through vents in the injection pins and along the parting line. Runner, gate and vent design are important to insure the mould is properly filled and the resin reaches all part of the mould in a uniform filling cycle.
Step 3: The Cooling Stage
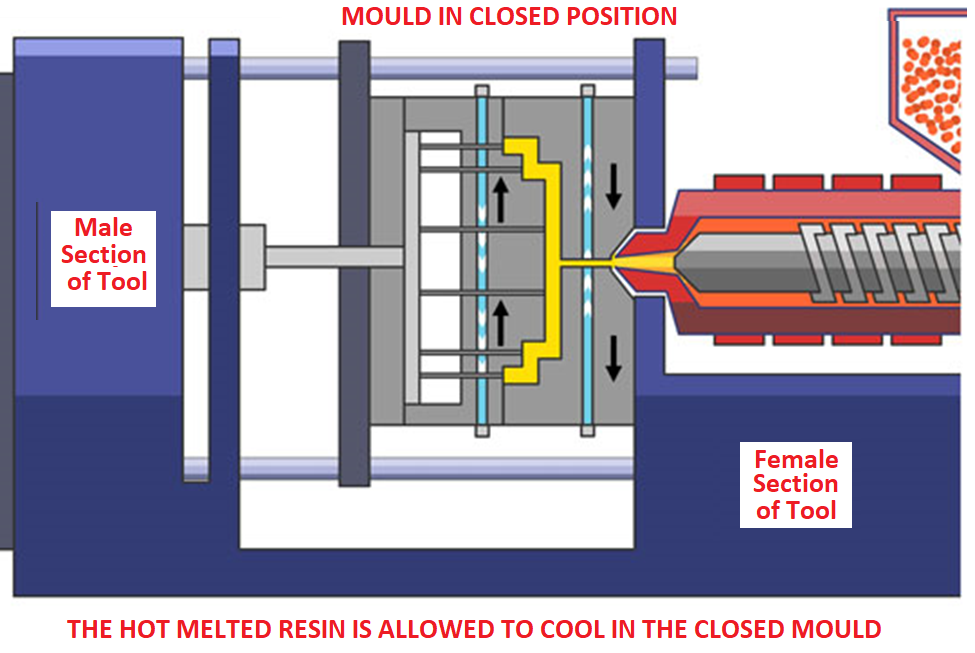
Once the profiled cavities of the mould is filled (marked in Yellow below, showing in this case a component, not a plastic box), the nearly finished box is allowed to cool for the exact amount of time needed to harden the material. Cooling time is dependent on the type of resin used and the wall thickness of the box. Each mould is designed with internal cooling or heating channels along which water is flushed through the mould to maintain a constant temperature.
Step 4: Plasticising the Resin Stage
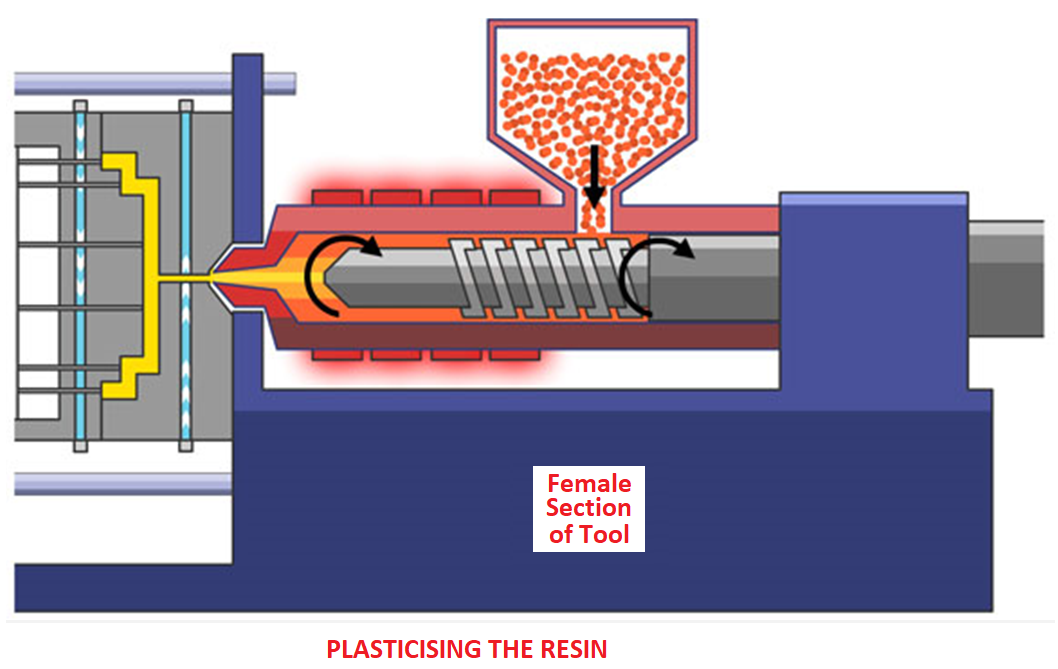
While the injection moulded box cools, the barrel screw retracts and draws new plastic resin into the barrel from the material hopper ready to produce the next box in line. The heater bands maintain the needed barrel temperature for the type of resin being used.
Step 5: Final Stage: Ejection of Finished Product
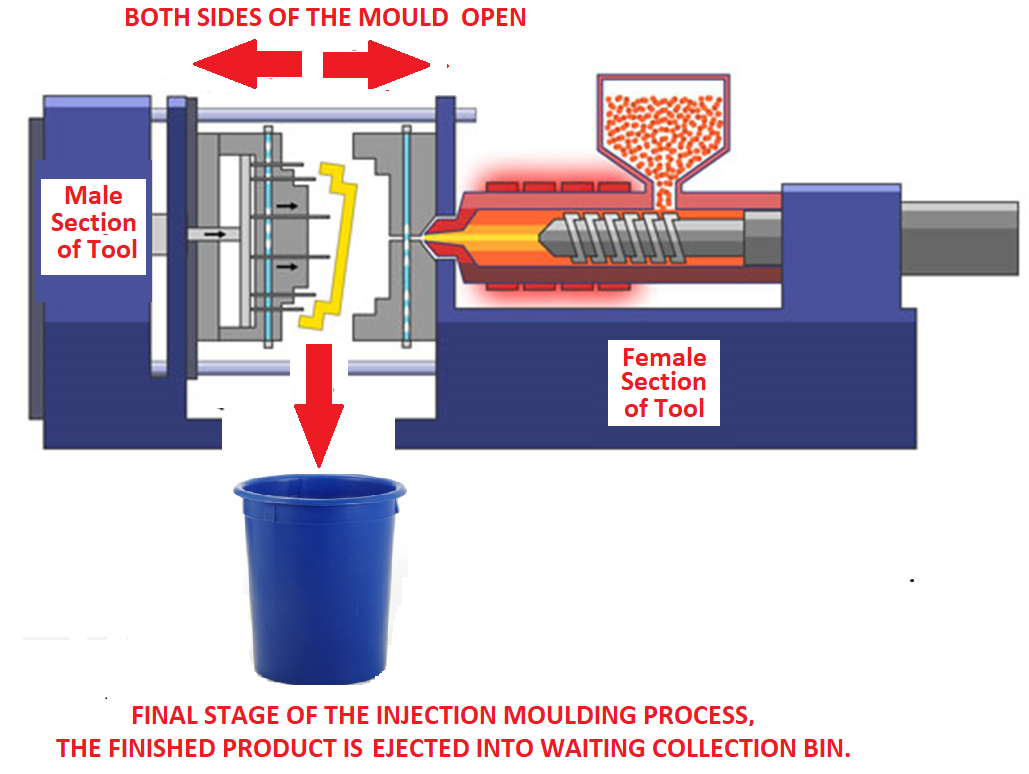
The mould opens and the ejector rod moves the ejector pins forward, allowing the then finished box to fall into in a bin located below the mould.
The useful Flowchart Style Illustration above, shows the basics of Injection Moulding and is provided by Aire Plastics of Texas https://www.aireplastics.com/basic-injection-molding-process, with some minor adjustments by us, to allow the visual explanation to accommodate those more interested in the production process of plastic boxes, rather than plastic components parts etc.
Understanding Plastic Boxes and Crystal Polystyrene: From Injection Moulding to Recycling
What do Crystal Polystyrene Granules look like?
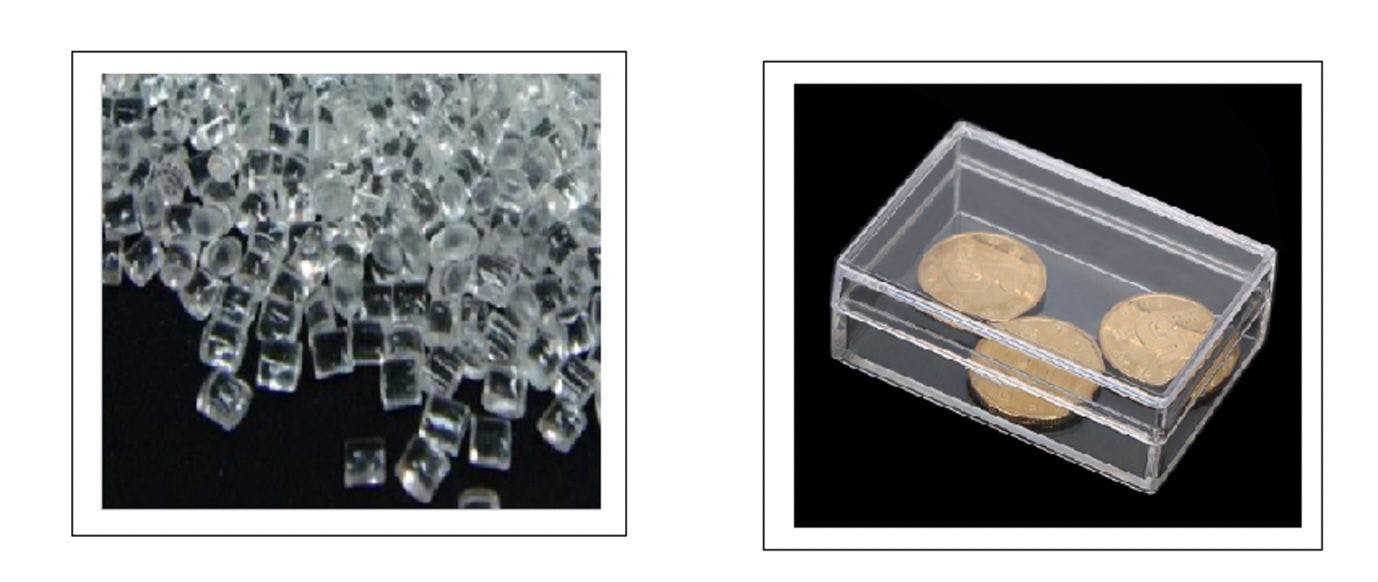
Injection Moulding is advantageous over many other processes because of the precision and high speed at which products can be made. No other manufacturing method of producing plastic boxes can match the quality and consistency of this process when molding plastic.
We hope the information provided above by Aire Plastics Texas has been useful and that you now have a better understanding of the basic Injection Moulding Process used to make plastic boxes.
Crystal Polystyrene Boxes - Protecting Fragile Contents
Custom-made foam inserts are available in a range of colors and densities and can be used to protect fragile items from accidental impact. Anti-static varieties of foam help prevent unwanted electrical discharges during transit.
Protective foam pads, with or without profiled cavities, can hold items in place and protect them from accidental damage.
Crystal Polystyrene Boxes - Can they be recycled?
Crystal Polystyrene is designated a recycling Category Type 6 and can be ground down, compacted, and manufactured into something new or recycled into a completely new product. Crystal Polystyrene Boxes are also reusable thanks to their sturdiness and longevity, and are therefore hardly ever discarded after their first use. They can be reused for storing personal items, keepsakes, household odds and ends, and all types of 'stuff'.
Crystal Polystyrene - Sustainability and the Environment
The raw material for post-consumer recycling relies on packaging waste that has been collected for recycling by the consumer and deposited in the correct dedicated recycling collection points.
The plastics industry is constantly searching for alternative plastic packaging solutions that are biodegradable or derived from more sustainable sources.
Polypropylene Boxes - Durable and Impact Resistant Plastic Packaging
(less brittle but stronger than Crystal Polystyrene, cloudier appearance)
What is Polypropylene ?
Polypropylene, commonly known as PP, is a type of thermoplastic polymer created by combining propylene monomers. It is widely used across various industries, including packaging for consumer goods, plastic parts for different applications, as well as in the medical, automotive, and aerospace sectors, among others.
Unlike Crystal Polystyrene, PP has a semi-opaque appearance and is lighter in weight. Due to its flexible nature, it has more give than Crystal Polystyrene, making it less brittle and more resistant to impact and accidental damage.
Polypropylene - Protecting FRAGILE Contents
Best solution is Bespoke Foam Inserts or Pads, as for Crystal Polystyrene Boxes detail above
Polypropylene - What Styles of Lid ?
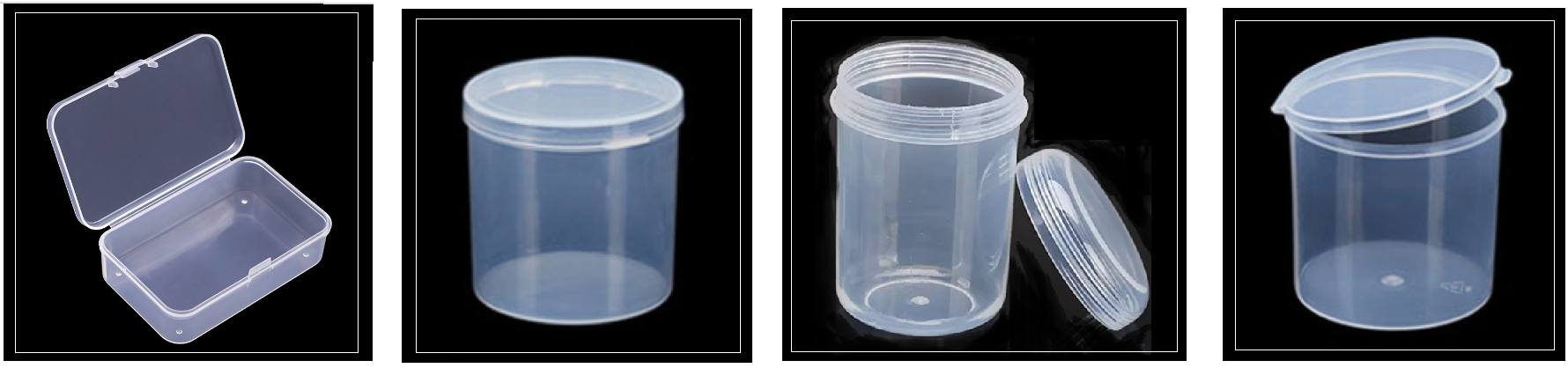
- Hinged
- Slip Lid
- Screw Cap
- Flip Top
Polypropylene - Print Options ?
Mainly the same as for Crystal Polystyrene ones, but not Holograms, Reverse Under Surface Printing or Laser Cut Self Adhesive Lettering. Logos etc
Polypropylene - How are they made ?
Polypropylene Boxes are made in exactly the same way as Crystal Polystyrene ones,
using the Injection Moulding manufacturing process.
What do Polypropylene Granules look like?
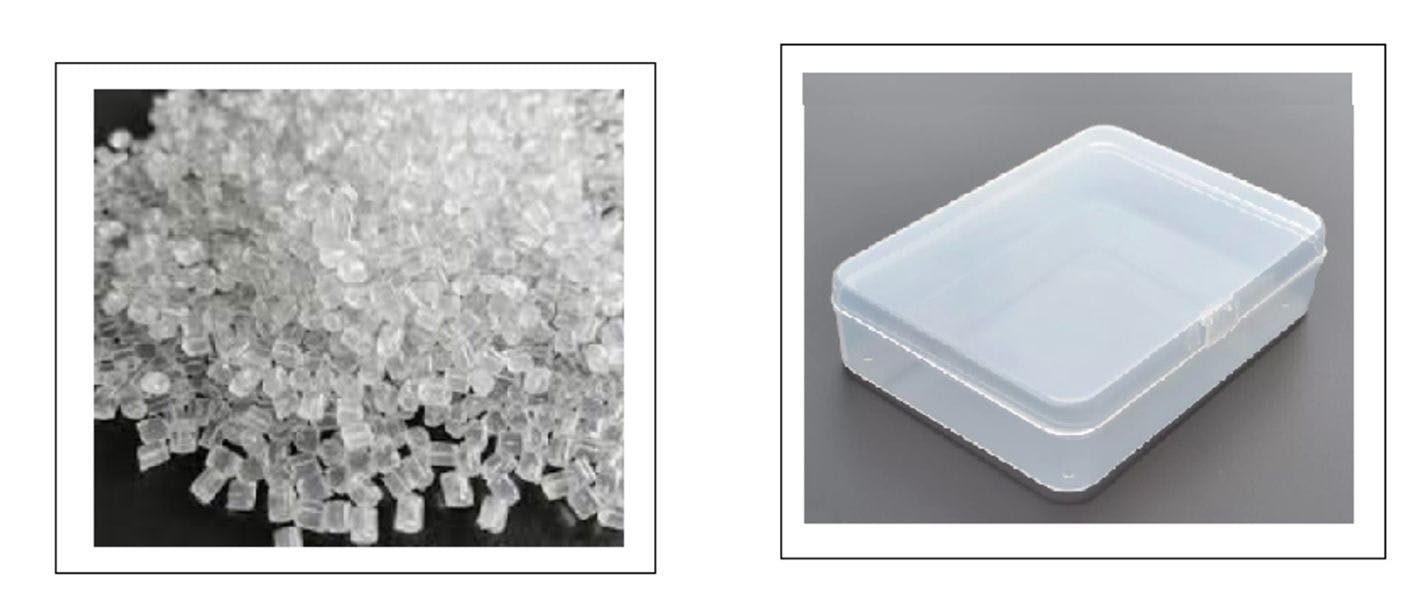
Polypropylene Granules Injection Moulded Polypropylene Box
Polypropylene - Can they be recycled?
Polypropylene is designated a recycling Category Type 5 and is recyclable. It can be ground down, compacted and manufactured into something new or remoulded or recycled into a completely new product. Polypropylene Boxes are also reusable thanks to their sturdiness and longevity and are therefore hardly ever thrown in the bin after their first use, so they can be re-used for storage of personal items, keepsakes, household odds and ends i.e. all types of ’stuff’.
The raw material for the post-consumer recycling, relies on packaging waste that has been collected for recycling by the consumer and deposited in the correct dedicated recycling collection points.
The Plastics industry is constantly searching for alternative plastic packaging solutions, that are biodegradable or derived from more sustainable sources.
Sustainability and the Environment
The Plastics industry is constantly searching for alternative solutions to plastic packaging, that are both biodegradable or derived from sustainable sources.
Acrylic boxes Glass Clear (Brand Name Perspex)
What is Acrylic ?
Acrylic is thermoplastic material made from Polymethyl Methacrylate, which is a vinyl polymer. It is part of the polymer family and is also known as acrylate, but for simplicity, it is called by the general term Acrylic. It is also known as PMMA or by Brand names such as Perspex, Plexiglas.
Acrylic is typically manufactured as sheets, rods or tubes. Almost unbreakable, polycarbonate key strength lies in its durability. It also has good resistance to high temperatures, is lightweight, being Half the weight of glass, but still offering High Impact Resistance too, so it is often used as a shatter-proof replacement for glass and can be used for a wide range of other purposes, as it is also easy to bend or form into shapes.
Acrylic - What styles of lid are available?
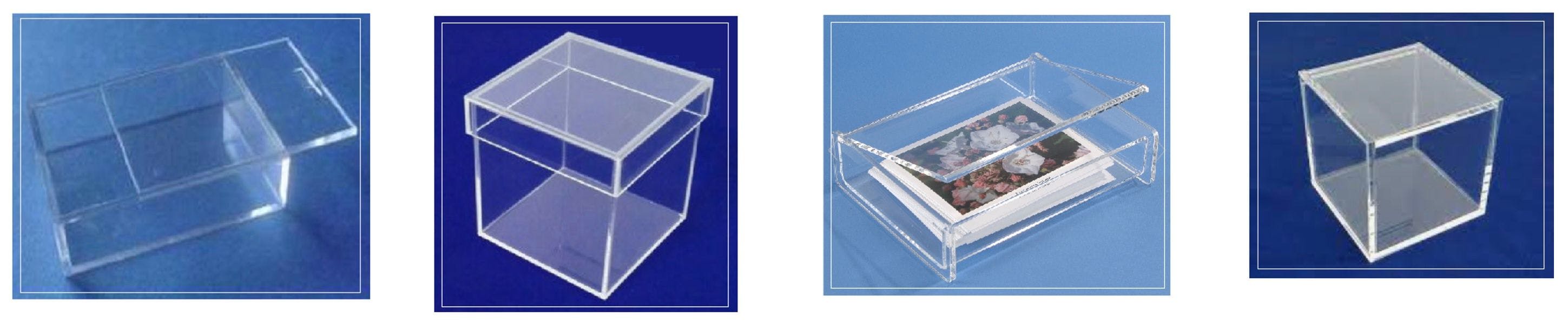
- Sliding Lid
- Cap Lid
- Hinged Lid
- Rebated Lid
Acrylic - Print Options ?
Mainly exactly the same methods as for Crystal Polystyrene ones
Acrylic - How are They Made ?
All Acrylic boxes are hand-made and hand finished, involving Laser Cutting, CNC Machining and Hand Polishing for a pristine appearance.
The types of equipment used to make custom bespoke Perspex/Acrylic boxes are 3000mm x 2000mm Flat Bed CNC routers and High Powered RF lasers with multi-directional heads, along with bending, polishing and finishing facilities. Computer software with advanced 3D design allows instant changes to your product. These large format machines allow easy transition to volume production. So if you require a one off or 10,000 units, we can help.
Acrylic – Recycling
Acrylic isn't biodegradable and is designated as a recycling Category Type 7. Therefore, it won't naturally decompose over time. While companies and manufacturers are keen to recycle acrylic, unfortunately, at the moment, many recycling companies do not have the facilities or expertise to safely and economically recycle acrylics.
Polycarbonate boxes
Glass Clear, Stronger than Acrylic, more expensive and less prone to scratching
What is Polycarbonate ?
Polycarbonate is another multi-functional substrate, with a high impact resistance. An alternative to Acrylic, Polycarbonate is strong and rigid, so is best served to protect against damage or where material has to be hard wearing. Widely used for Presentation Packaging and Transit or Storage Boxes, Machinery Guards etc.
Polycarbonate - What Styles of Lid
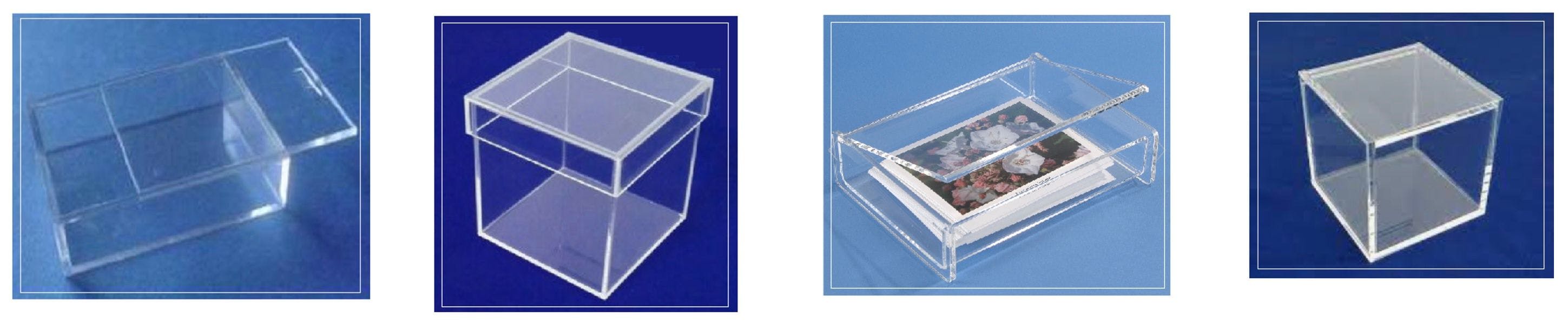
- Sliding Lid
- Cap Lid
- Hinged Lid
- Rebated Lid
Polycarbonate - Print Options ?
Polycarbonate can be Silk Screen printed, Pad printed, Hot Foil Stamped or applied with self-adhesive Vinyl Letters, or logos etc
Polycarbonate - How are they made?
Like Acrylic, all Polycarbonate boxes are hand-made, using exactly the same methods as for Acrylic ones above.
Polycarbonate - Print Options ?
Polycarbonate can be Silk Screen printed, Pad printed, Hot Foil Stamped or applied with self-adhesive Vinyl Letters, or logos etc
Polycarbonate – Recycling
Like Acrylic, Polycarbonate isn't biodegradable and is designated as a recycling Category Type 7. Therefore, it won't naturally decompose over time. While companies and manufacturers are keen to recycle Polycarbonate, unfortunately, at the moment, many recycling companies do not have the facilities or expertise to safely and economically recycle Polycarbonate.